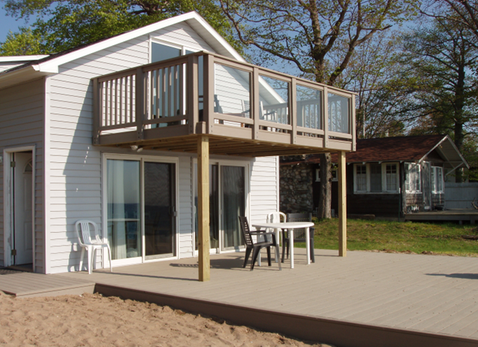
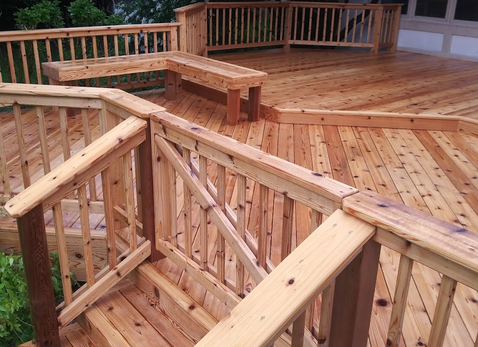
What makes Deck Shine different?
- Meticulous construction of a well-thought-out plan.
- Because we provide refinishing services in addition to building decks, we have literally seen thousands of decks built by other people. We have seen it all over the last 30 years. We know what works and what doesn't work.
- When we accept your project, we are all in. We will work closely with you to create a one of a kind masterpiece that is tailored to your specific needs. Every project is unique. We go for the ultimate "Wow!" factor on every deck we build.
- We don't install a deck. We build your deck. Deck building is a highly specialized trade that requires conscientious, experienced craftsmen. Our deck building methods have evolved over the last 30 years. Very few builders come back in ten years to see how their project has performed. We track our builds over many years and have adjusted our methods accordingly. It's shocking to see the simple mistakes builders make that cause decks to fail. Every deck we build is guaranteed for life!
- The key to building a deck that lasts forever lies in how the frame is constructed. Your deck must be framed to get plenty of air flow and to drain through at all connection points. This includes the elimination of areas for debris and moisture to collect. We call it "venting". Decks that stay wet all the time will fail. However, whether it's constructed with wood or composite...
A properly framed "vented" deck will last a lifetime and beyond.
What makes a Deck Shine deck special?
The secret to a deck that lasts forever lies in how it is framed.
We frame every deck for maximum drainage. We do not create unnecessary areas for moisture and debris to collect. A deck that fully dries between rain events will not only last much longer, it will perform better, attract less mold and insect activity, stay cleaner and be much easier for you to maintain. Simply put, any water that lands on your deck should be able to drain through at ALL connection points (ends of boards/between boards).
A deck that stays wet will attract mold growth and fail prematurely.
Your deck didn't fail because it's wood. It failed because of the way it was framed. Your old deck wasn't "vented" properly.
- Moisture--Decks that stay wet will fail, regardless of the material used in construction. Almost immediately after construction any wet areas will attract mold growth.
- Mold Proliferation--Mold will eventually root into and embed itself into your deck boards. Even composite materials will get moldy if allowed to stay wet. Keep in mind, most composites are pressed or extruded material with a PVC cap. If you look at the end of a composite board you can see that there are two different materials. The core is a pressed material (usually recycled wood and plastic).
- The Freeze/Thaw Cycle-- In late Fall and early Spring, water trapped in your deck will freeze each night and thaw each day. This freeze thaw cycle will wreak havoc on your deck.
Common Deck Building Mistakes
Portfolios of other Michigan deck builders show numerous examples of these mistakes!
The following are examples of common deck problems. Sadly, these decks were doomed from day one. But with some simple changes to the way the decks were framed, these issues could have been avoided. All deck problems can be traced to the connections where boards meet other boards (i.e. wood meets wood, wood meets composite, or composite meets composite). If allowed to "vent" and dry out completely between rain events, mold won't proliferate and break the material down.
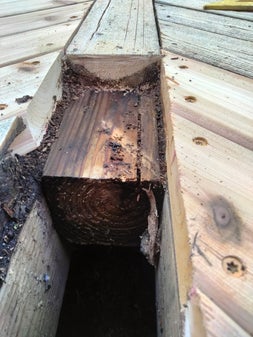
Deck floor view with one board removed.
This photo was taken on a completely dry summer day in Michigan. Notice the U-shaped wetness on the bottom of the top deck plank. Rainwater is unable to drain through, so it sits on top of the structural member and rots the deck board from the bottom up. Couple that with tight joints and you have a recipe for disaster. This is the number one reason decks fail! It's clear that the builder used scrap lumber as a "nailer". It is very common for builders to use cutoff scraps as nailers and blocking underneath the deck. It can be okay to repurpose materials. But using scrap cedar decking as blocking under the deck, for example, is not okay. Only pressure treated lumber or other weatherproof material should be used for framing.
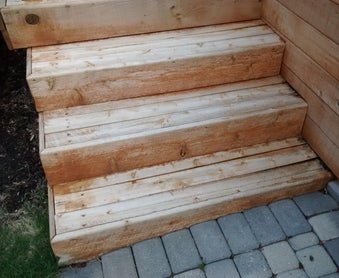
At first glance, this appears to be a fine set of stairs. However, there are multiple problems with this staircase!
1.The biggest problem is that right side of the staircase is running under the wall. If you look closely you can see that the right side of steps are wet. Once again, this photo was taken on a completely dry day. The 2x4 deck planks have succumbed to the freeze/thaw cycle and the ends are rotted on the right side.
2. Rough sawn 1x6 was used as trim around the deck and steps to cover the end cuts. This locks moisture, leaves, seeds, and other debris around each step, thus rotting the ends and along the face of each step.
3. The cedar fascia board runs behind the brick pavers. This will rot the fascia.
4. The staircase needs a railing (preferrably on both sides), but the way it was planned/framed there is no easy way to attach a railing now!
5. Each step is a different height, turning a simple trek up or down into an unpredictable adventure!
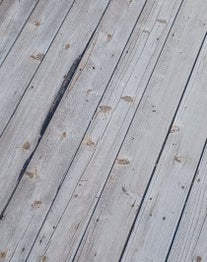
It is common for deck builders to affix the deck floor planks tightly together. The idea is that as the boards dry out they will shrink and you will end up with a sufficient gap between the boards for air flow. In reality the opposite is true. Because there is no gap, the boards stay wet and actually swell, making them even tighter than they were at the time of installation.
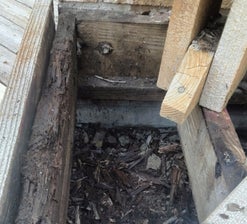
Left side of photo shows a cedar joist with extensive rot visible along the top (cedar floor planks removed). The next joist over to the right is pressure treated lumber. It is in perfect condition, even after 34 years. The entire understructure of this deck was constructed with pressure treated lumber except for the outside joist. The only reason the builder used cedar joists around the outside of the deck is for aesthetic reasons. Treated lumber has a slightly different look when stained, so the builder used cedar so it would match the rest of the exposed lumber. Always frame with treated lumber and then face it with your decking. Never frame with your finished decking.
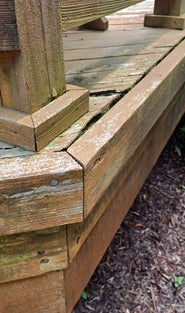
This is the view around the perimeter of the deck. You can plainly see that the outer edge of the deck has completely rotted. It's easy to jump to the conclusion that the deck rotted because it is made of cedar instead of pressure treated lumber or composite decking. But in reality, it rotted because it was framed incorrectly. When building a deck, it's important to frame with pressure treated lumber and then "face" the frame with your choice of decking. Also, the trim around the posts is not only unnecessary, but it caused the decking and the posts to rot. The 2x4 trim that covers the end cuts also added to the problem. These areas never completely dry. The wood stays wet and causes decay.
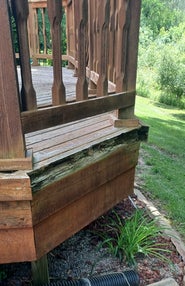
This is the same deck with the 2x4 trim board removed. This is what happens when you don't frame all connection points (areas where wood meets wood) to vent. Rainwater must be able to drain all the way through the deck. The second issue is that you can't use non-pressure treated lumber as a structural member. After making the first two mistakes, the builder topped it off by adding another 2x4 around the deck floor and trimming each post.
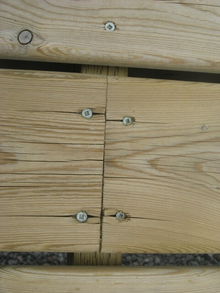
When this builder screwed the end to end (butt) joint, he or she split the end of the board. After splitting one board, did they get their drill out and predrill a pilot hole to prevent splitting the next one? No!...They continued to split every butt joint on the deck. There is simply no excuse for this!
There is a second problem here. Because most decking is a maximum of 16 feet long (it's getting progressively harder to find decent 20's these days), some type of seam is required to reach from one side of the deck to the other. It is common for builders to make random seams all over the deck floor where two boards share one joist. Water will seep into the gap between the ends of the planks and sit on the top of the joist underneath. The area will stay wet, collect gunk and cause future problems.
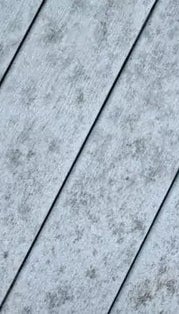
Most composites use wood flour mixed with plastic pressed together with a bonding agent. These materials are porous and will grow mold if allowed to stay wet. If you have an earlier version of composite decking, it is recommended that you stain/seal it with a penetrating oil stain. It can be difficult for folks to wrap their brains around this concept. The composite decking manufacturers have spent considerable resources convincing us all that their products need no sealing. These composite materials will benefit from a similar restoration process used on natural wood. If you have one of these earlier composite decking materials (that does NOT have a plastic veneer coating) and it has mold stains or is continuing to swell and loose its shape, then it needs to be refinished using our 5 Step Power Washing Process.
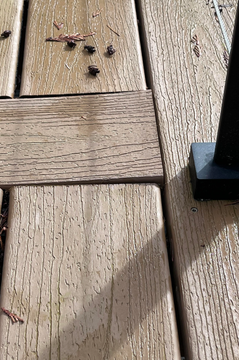
Trex Ski Tips
This photo was taken from a Reddit post titled Composite boards curving up at ends. Is this inevitable? Can it be fixed? Deck Shine recommends reading this post!
Most top-tier options now consist of a pressed wood fiber/recycled plastic "core" wrapped in an all plastic outer veneer. There are also all plastic options and some cementitious options have recently hit the market. Plastics are typically more susceptible than wood to expansion and contraction over time, but the composite decking industry is constantly improving and they have made great strides in this department. While it isn't exactly maintenance free, it does require less maintenance than wood.
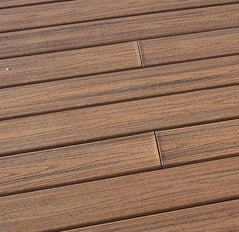
Swelling and delamination of the outer plastic coating
Composite lumber can swell at the ends, especially when seams share a single joist. Water that cannot drain through will sit in the joint on top of the joist and cause the end cuts to swell. The photo to the left depicts a common complaint with the newest composite boards (composite core with a virgin PVC cap). This problem can also be caused by not leaving an expansion joint (gap) at the end of each board. Even if you are using composite decking, you should still frame your deck so it gets proper air flow and drains through at all connection points.
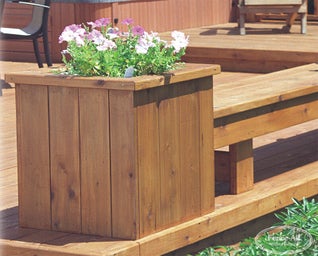
Building items into your deck
Built in planter boxes look nice, initially. But come back 7 or 8 years later and you will have a much different opinion. If you want planters, it is much better to find a plastic container or insert and then build around it. The mistake here (in the photo) is that the deck was completed first, then the planter was built to just sit on top of the finished deck. Or even worse, complete the deck, build the planter, and simply screw it down to the deck surface. Your deck will collect debris around the perimeter and under the planter itself causing the area to stay wet. If you really want built in planters, then the deck must be framed up to and around the planter. The finished decking should not run under the planter.

Running your lower section under your upper section is a mistake.
Frame for lower deck should end, then the step is framed. In this case, the lower deck was completed and then a step was built directly on top of the finished lower deck. The second pic shows the exact same deck during rebuild. Notice how the lower deck frame ends at the step. The end cuts will drain off and dry out between rain events, greatly increasing longevity.
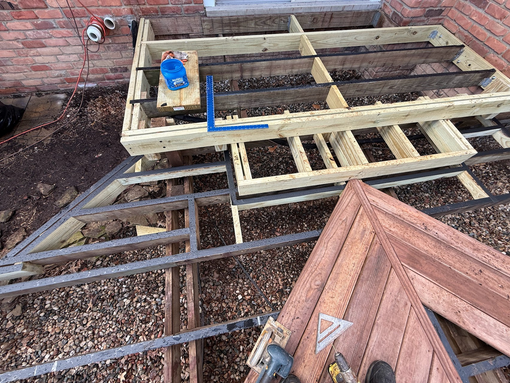
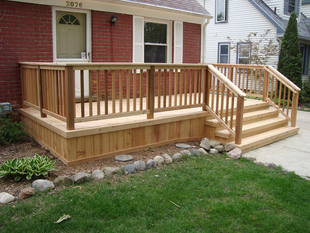
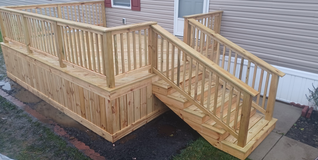
Side by Side comparison...
Deck 1: A different experienced builder (will need to be replaced in 10-15 years)
We can see that the builder did a nice job constructing this cedar deck. However, this cedar deck will rot prematurely. This deck was built with a total disregard for the idea of "venting". If the builder had even considered the idea of air flow, they would have installed the skirting with some gap in between--not tight together. Also, using the 2x4 fascia board to cover the end cuts will keep the ends of the boards constantly wet.
Deck 2: Deck Shine (will last indefinitely)
Our deck is very similar, except that it happens to be a less expensive pressure treated option instead of cedar. Constant air flow in and around the deck is critical, so we installed our skirting with 1/4" gap between each board. Also, our fascia board runs under the "vented" picture frame. This deck will dry completely between rain events, which makes an enormous difference in how long it will last.
The 2 decks pictured above look surprisingly similar when built, but in a few short years the difference will be readily apparent. The top deck will need to be replaced, but the Deck Shine deck will last much longer--because it is built for maximum air flow and all connection points are "vented". The Deck Shine deck will dry between rains, stopping mold and insect activity before they start; thus, making it easier to keep clean and adding decades to its life span.
What sets Deck Shine apart from other builders?
Over the last 30 years, we have seen thousands of decks built by other builders. We see what has worked and what has not worked. The situations described above must be avoided. Give water a way to drain through at all connection points. Very few builders come back in 10 years to see how the deck they built has held up. Because we also provide deck maintenance services, we constantly get to see other builders' work. We also get to track our own deck builds over many years--even decades. The "vented" framing method not only works, but it is the only way to ensure that you don't have the problems described above. Even if you use the latest version of composite decking, it still must be framed to drain through at all connection points ("vented").
How do you frame a deck to "vent" so water can drain all the way through and it will completely dry between rain events?
Create sections with planned seams using Picture Framing...
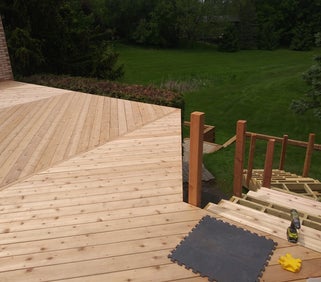
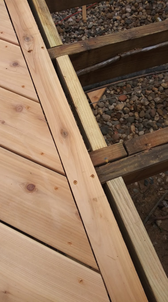
Typically, your deck will require some sort of seam or end to end (butt) joint because a single board will not reach across the entire deck. Often times we will see these seams placed randomly throughout the floor where two boards share one joist. Water will sit on the joist and keep the ends of the floor planks wet. It is critical for all end cuts to get air flow. This is achieved by using a picture frame pattern (pictured left). Notice the blocking that will support the next section of flooring. Rainwater will drain through at the ends of the boards. By using a couple extra joists or blocking between joists, all end cuts will vent and allow rainwater to drain through.
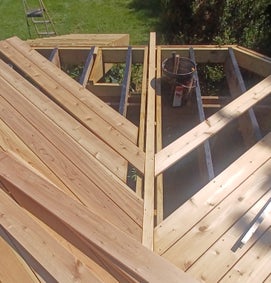
Venting:
Because a single board will not reach from one side of the deck to the other side, it will require a seam in the floor. All seams should be planned and framed accordingly. You do not want random seams all over the deck (similar to an interior wood floor) where the seam includes two boards on a shared joist. The end of the board should hang over the joist slightly, allowing air to circulate around the end of the board.
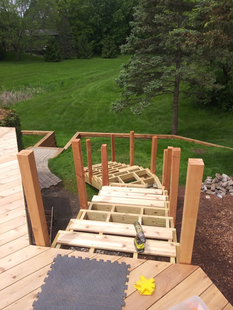
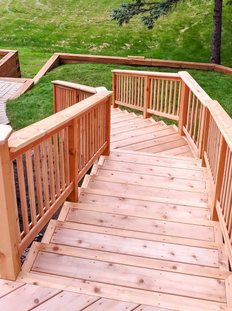
Each step is also picture framed. Not only does it look beautiful, it allows the end cuts to be vented, just like every other end cut on the deck. Constant air flow on the ends of the boards is absolutely critical to prevent future problems. Water and small debris can pass through instead of sitting in the joint and remaining wet all the time.
Composite Deck Installation
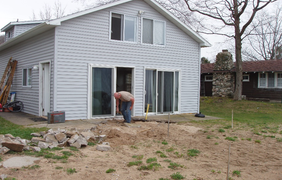
Scope of project:
Install 500 square foot main deck below. Remove 2 top windows and install sliding patio doorwall and install top lakeview deck. The top deck was created so that one section of railing could be easily removed and a staircase later added without completely tearing the deck apart and starting over.
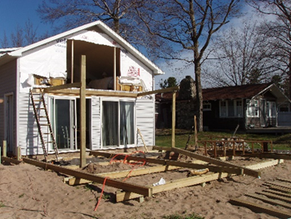
Top windows now removed. Framing for doorwall taking shape. 4x6 posts installed for upper deck. Three post and beam sets (with a ledger on the building) were used to support a 2x6 joist frame. Many clients are concerned with joist size. Joists can be any dimension, as long as they are properly supported by the correct post and beam system underneath. In this case, three beams were needed to support 2x6 joists. If the joists were 2x8, then two beams sets would have been required. If we had used 2x10 or 2x12 joists, then perhaps only one beam set would be required (with a ledger attached to the building. So any joist size can be used, as long as they are sufficiently supported by the appropriate beam sets!
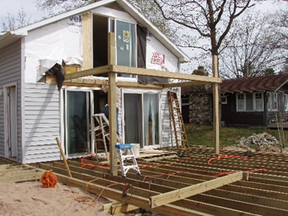
Doorwall in. Lower joists set. Upper frame taking shape.
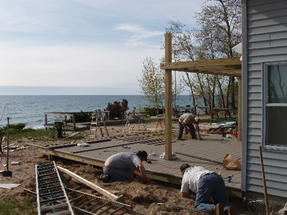
Lower deck nearly installed. Rodent barrier being installed around perimeter of deck,
Note: Any galvanized wire fabric (chicken wire) can be used for this purpose. If you have current rodent activity, it is quite difficult to keep them out. Your barrier must be buried a foot down and a foot out from the deck perimeter, or the little guys will simply dig under the barrier to get "home"...If you do NOT have current rodent activity then it's much easier. You just have to make it difficult enough and they will move on. An improper rodent barrier will provide safe haven for small animals. A proper barrier must be completely sealed.
Completed Deck with doorwall and see through glass panels
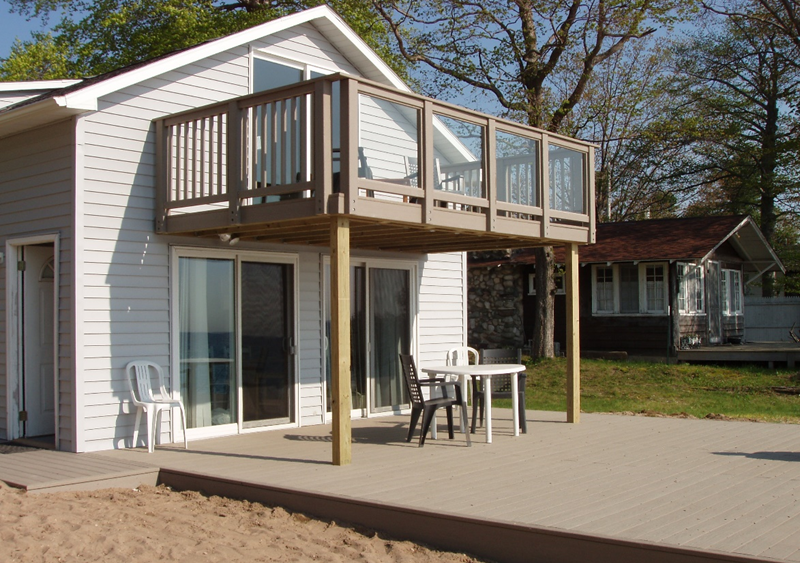